FAMU-FSU College of Engineering researchers use artificial intelligence to improve defect detection in powder-based 3D printing
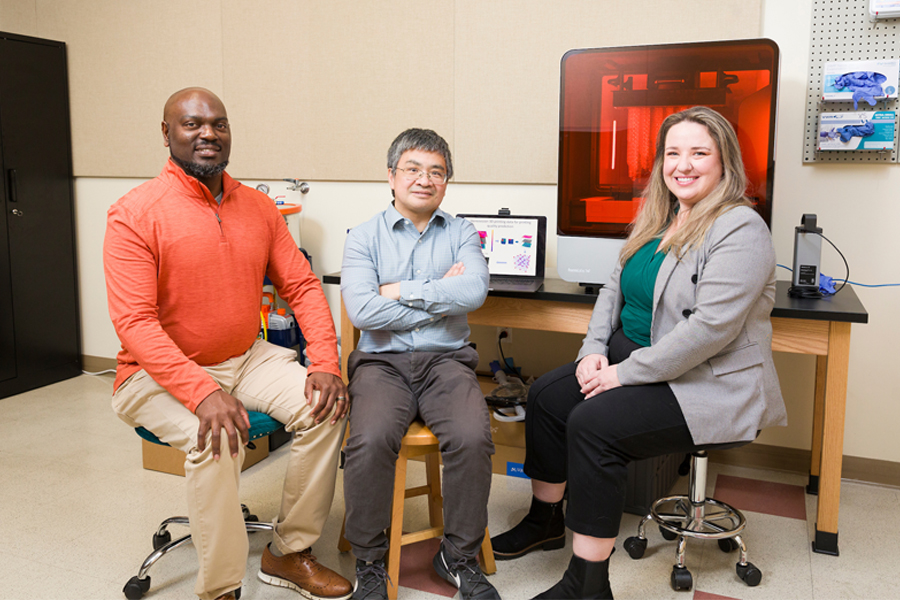
Researchers at the FAMU-FSU College of Engineering are using artificial intelligence to create new tools that can help find defects in powder-based 3D printing for a $2.2 million project supported by the Air Force Office of Scientific Research, or AFOSR.
Additive manufacturing, also known as 3D printing, holds the potential to transform manufacturing and prototyping. Powder-based fabrication is a 3D printing method in which material in powder form is bonded together to create solid functional parts.
In a project led by Hui Wang, an associate professor in the Department of Industrial and Manufacturing Engineering, FAMU-FSU engineers will collaborate with researchers at Pennsylvania State University and HP Inc. to use combinatorial generalization, or CG, to improve the accuracy of models used for predicting defects in 3D printing.
“Combinatorial generalization represents a computational reasoning capability that supports next-generation AI by mimicking human recognition behavior that generates new knowledge from data,” Wang said. “It is exciting to use this emerging technology to solve difficult manufacturing puzzles.”
The project is focused on binder jetting, a 3D printing technique that uses a liquid binder to stick powdered materials together. The technique is essential for creating high-performance components with intricate geometries and is capable of higher productivity than other metal printing technologies.
WHY IT MATTERS
Powder-based fabrication is used in many industries, including aerospace, automotive, health care and the military to make complex metal components.
One of the challenges in powder-based fabrication is understanding how the material becomes porous, or filled with tiny holes, a common defect resulting from powder spread and powder-droplet interactions.
To solve the problem, the researchers will use the developing artificial intelligence tool combinatorial generalization, which can empower the AI to make inferences on new scenarios given piecewise knowledge learned from multiple data sources.
An example of CG in people might be a designer who draws inspiration from existing work to create something entirely new or a doctor who analyzes a patient’s symptoms and medical history to recognize patterns that suggest a specific illness, even if they haven’t encountered the exact case before. The approach showcases how existing knowledge and patterns can lead to innovative solutions in additive manufacturing.
By recognizing patterns and relationships, the project promises to deliver innovative CG tools to investigate defects that are typically difficult to detect. The potential benefits extend beyond manufacturing with system maintenance and cybersecurity applications.
“This technology could democratize manufacturing, making it easier for inexperienced manufacturers to advance from lab testing to large-scale production,” Wang said.
COLLABORATION AND STUDENT SUCCESS
The research led by Wang’s team significantly benefits from graduate students, postdoctoral researchers and faculty collaborators Tarik Dickens and Rebekah Downes from the Department of Industrial and Manufacturing Engineering. Jun Zeng, who leads the Physics AI engine group in the additive manufacturing R&D Lab at HP Inc., and Penn State University Professor Jingjing Li are also collaborators on this initiative.
Funding from the AFOSR will help the researchers obtain essential experimental materials and small-scale testing equipment for the college. The Penn State research team is providing essential simulations and XCT data modeling to support FAMU-FSU engineering researchers.
In partnership with HP Inc., the initiative is on target to provide essential training and development opportunities, including access to data from HP’s 3D Printing and Digital Manufacturing Center of Excellence, high-performance computing resources and student internships. In addition, FAMU-FSU doctoral and undergraduate students have served as HP interns.
NEXT STEPS
The project shows the potential of interdisciplinary work that brings together expertise in industrial and manufacturing engineering with the new capabilities offered by artificial intelligence.
“AFOSR programs in computational mathematics and physical sciences are actively seeking novel solutions in machine learning for scientific discovery, and our project aligns well with this vision,” Wang said. “We expect that our discoveries will significantly enhance the ability of Department of Defense researchers to efficiently leverage a variety of data sources and expedite the development of new manufacturing processes and materials. It’s exciting to see what lies ahead and where this research will take us in the future.”
The post FAMU-FSU College of Engineering researchers use artificial intelligence to improve defect detection in powder-based 3D printing appeared first on Florida State University News.